Pump Packing Solutions for Oil & Gas: Enhancing Efficiency and Safety
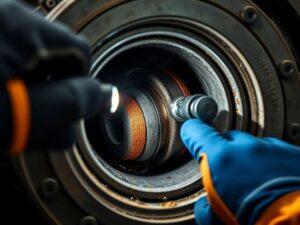
In hydraulic fracturing, sealing reliability isn’t just about containment—it’s about continuity. A single overlooked pump packing ring can shut down a stage, halt progress, and send costs soaring. These aren’t hypotheticals. They happen. And more often than they should. The irony? Pump packing is one of the smallest components on-site—but when it fails, it demands the biggest attention.
You already know that frac pumps and blending units face relentless pressure. Literally. And the pump packing rings holding it all together? They’re the quiet heroes—until they aren’t. For a Maintenance and Reliability Manager, pump packing isn’t a background detail. It’s a frontline safety and efficiency tool.
This guide cuts through the noise. It zeroes in on how the right pump packing choices—from materials to maintenance—drive real-world outcomes: uptime, safety, and operational consistency.
Understanding Pump Packing in Frac Operations
At its core, pump packing is a collection of compression rings. These sit in the stuffing box, hugging the shaft, containing aggressive, high-pressure fluids while accommodating shaft movement.
Mechanical seals? They’re often reserved for cleaner jobs. Not frac. Here, abrasion, chemical exposure, and temperature fluctuations make compression packing the logical choice.
And in that stuffing box? You’ve got more than just packing. Seal wear rings. Glands. Support hardware that works in sync. But even the best system breaks down if the packing can’t hold its line.
There’s another silent culprit: shaft condition. Scored, pitted, or out-of-round shafts destroy even the best pump packing. Routine inspections, refinishing, and tolerancing checks aren’t optional. They’re essential.
Consistent performance—minimal leaks, stable operation, longer service life—signals that everything’s working. But the moment you see unexpected drip lines or hear chatter from the gland? It’s already costing you.
Choosing the Right Packing Material for Harsh Conditions
Every frac site is its own battleground. Slurry abrasiveness, chemical extremes, and punishing heat cycles demand materials that can take a hit and keep sealing.
Here’s a breakdown of the big three:
- Graphite: Great thermal conductivity. Chemically inert. But go too brittle, and you risk fracture under high shear.
- PTFE: Think chemical resistance and low friction. But it needs reinforcement—glass, carbon, or graphite fillers—to survive pressure.
- Aramid Fibers: Tough against abrasion. Withstand pounding proppants. Still, without proper lubrication, they can overheat quickly.
But there’s nuance. Is your fluid loaded with sand? Expect erosion. Are you seeing pH swings? Look for chemical breakdown. Have biocides or corrosion inhibitors in play? Some materials won’t survive the week.
That’s why many pump packings are hybrid builds—mixing aramid corners with PTFE-graphite centers. They’re engineered to handle the extremes. Still, sometimes you don’t need the Cadillac. For short jobs or milder fluids, standard grades can be a smart, cost-conscious fit.
Choose based on:
- Pressure load and cycle speed
- Fluid chemistry and abrasiveness
- Expected runtime and downtime intervals
Your goal? Get it right the first time—then get repeatable results.
The Hidden Link Between Packing and Operational Safety
Let’s talk risk. Because when packing fails, it’s rarely quiet. Leaks create slicks. Fluids spill where they shouldn’t. And vapor releases? Those don’t just smell bad—they can trigger alarms and audits.
You’ve seen the aftermath: crews scrambling, job halted, compliance officers on high alert.
Most issues trace back to improper torque. Too loose? You leak. Too tight? You burn. Then there’s extrusion, where the packing literally shoots out due to excessive clearance or spike pressure. Or slow chemical degradation, silently turning robust rings into mush.
Add in thermal cycling—heat that cooks the gland over time—and you’re running a tightrope.
Yes, API 674 and ISO 13710 offer inspection guidance. But most safety comes down to vigilance. Field-level SOPs, proper walkdowns, and understanding the limits of each pump packing set. You know what’s on the line. It’s not just equipment.
Installation and Maintenance Best Practices
Here’s the truth: most pump packing doesn’t fail because it’s bad. It fails because it’s poorly installed.
Top mistakes?
- Over-torquing the gland. Like grinding your brakes until they glow.
- Skipping the staggered joint alignment. One shortcut, and you compromise the seal.
- Ignoring the warm-up run. Pump packing needs time to seat. Rushing this means accelerated wear.
Break-in isn’t just formality. It’s functional. You want just enough leakage to lubricate and cool. Not gushing. Not bone-dry.
Installation should look like this:
- Light initial compression
- Check under pressure
- Adjust gradually as the pump packing settles
Don’t forget support hardware. Lantern rings manage flush fluids. Junk rings absorb debris. Anti-extrusion rings block packing blowout. It’s a system, not a standalone fix.
When everything’s working? You see it. Cool glands. Stable pressures. Pump packing that lasts more than just a handful of hours.
What to Look for When Selecting a Packing Solution
Spec sheets don’t tell the whole story. They never do.
If you’re sourcing pump packing, ask:
- Is this rated for my fluid chemistry and pressure class?
- Are the braids tight, uniform, lubricated?
- Is it reinforced to handle my application’s real-world abuse?
And what about the vendor?
- Can they show test results under frac-like conditions?
- Do they offer traceability? Certifications?
- Will they support install training or post-job diagnostics?
The best suppliers don’t just ship product. They help you make it work.
Conclusion
Pump packing isn’t filler hardware. It’s foundational. It separates performance from breakdown, compliance from citations, and profit from sunk cost.
Choosing the right material. Installing it with care. Monitoring it with intent. That’s how you extend runtime and avoid unpleasant surprises.
Every leak avoided, every callout skipped, every frac stage completed without interruption—those are wins that start with better pump packing decisions.
Key Takeaways:
- Don’t underestimate the material blend: graphite, PTFE, aramid all behave differently under heat and pressure
- Smart cost control includes knowing when a standard pump packing is “good enough”
- Safe operations depend on consistent sealing—and that includes shaft condition, gland health, and correct torque
- Partner with vendors who back their product with data, not just specs
You don’t need perfection. You need predictability.
Frequently Asked Questions (FAQs)
Q: How can enterprises evaluate the ROI of investing in premium pump packing solutions?
A: ROI shows up in the numbers: fewer leak calls, longer replacement intervals, and less time spent tightening glands mid-job. When MTBF improves and sleeve wear drops, the value becomes obvious.
Q: What cross-functional teams should be involved in packing selection and maintenance planning?
A: Bring in Maintenance, HSE, Procurement, and Ops. Each sees a different side of the problem. Together, they cover everything from budget to boots-on-ground experience.
Q: Are there specific standards or guidelines for packing inspection in oilfield operations?
A: Nothing pump packing-exclusive, but broader specs apply. API 674 and ISO 13710 include key reliability checkpoints. Most real-world guidance comes from internal SOPs and hands-on inspections.
Frequently Unasked Questions (FUQs)
Q: What are the strategic consequences of treating packing as a consumable rather than a performance component?
A: You end up chasing symptoms, not solving root causes. That leads to budget blowouts, equipment wear, and eroded trust in the reliability program.
Q: How does packing failure affect the credibility of the entire reliability program?
A: One persistent leak undermines everything. Stakeholders stop believing in the systems meant to prevent failure. Confidence drops. So does support.
Q: What long-term risks emerge from choosing the wrong packing vendor?
A: Inconsistent quality. No traceability. Poor post-sale support. These risks pile up over time, draining budgets and exposing teams to compliance gaps.
Leave a Reply