Comparing Pump Plunger Materials: Tungsten Carbide vs. Stainless Steel vs. Ceramic
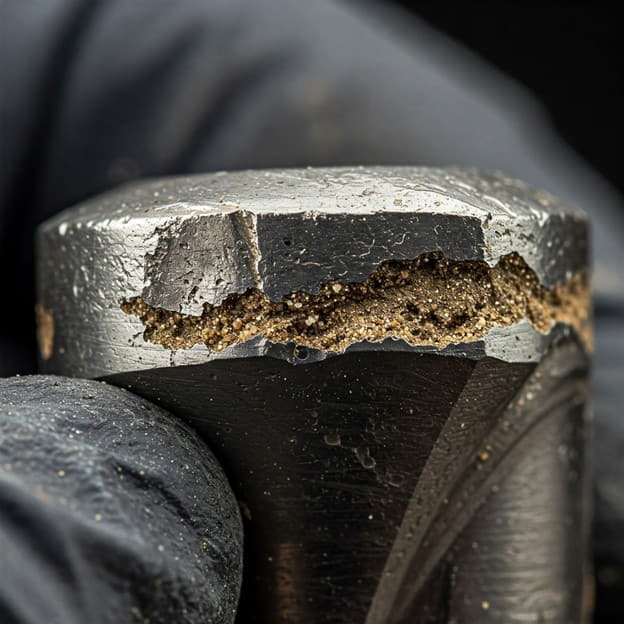
Unplanned pump failures in upstream operations aren’t just inconvenient — they’re costly. For a single high-pressure fracking site, the cost of downtime can easily reach six figures per day when factoring in deferred production, crew costs, and rescheduling penalties. One of the most overlooked — yet fundamentally critical — factors behind plunger failure is the material itself. In harsh drilling environments, the right material choice can extend operational life, while the wrong one can trigger cascading system failures.
From an operational standpoint, pump plungers face extreme loads, corrosive chemicals, and abrasive slurries — all while operating under intense cyclical stresses. Field engineers and procurement teams increasingly recognize that pump reliability isn’t just about pump design, but the microstructural integrity and chemical resilience of the plunger material. This article breaks down three widely used materials in upstream operations — Tungsten Carbide, Stainless Steel, and Ceramic — and compares them across critical performance factors relevant to oilfield professionals.
Material Science Fundamentals for Pump Plungers
Pump plungers in oilfield applications endure a convergence of severe operating conditions. Material selection must account for:
- Mechanical Stress: Reciprocating plungers endure high-frequency compression, tension, and torsional forces. Tensile strength and fatigue life are essential.
- Thermal Loads: Temperature swings — often from ambient to >300°F — can induce thermal shock, especially during startup/shutdown cycles.
- Chemical Compatibility: Exposure to chlorides, hydrogen sulfide (H₂S), and acidic completion fluids can degrade materials with poor corrosion resistance.
- Erosive Wear: Drilling muds frequently carry sand, cuttings, and proppant, accelerating plunger surface degradation under boundary lubrication.
In upstream oil and gas, it’s not just about surviving these factors individually — it’s about thriving under all of them simultaneously.
Tungsten Carbide Plungers: Performance Analysis
Tungsten Carbide (WC) is often the first material evaluated for high-wear environments. Its popularity stems from extreme hardness — typically exceeding 1400 HV (Vickers Hardness) — and exceptional dimensional stability under load.
The performance of WC plungers depends largely on the binder content, commonly cobalt (Co). A typical 6–12% Co content balances hardness and fracture toughness. Lower cobalt levels increase hardness but make the material more brittle — a key trade-off when operating under shock loading or rapid pressure cycling.
Advantages:
- Outstanding abrasion resistance in sand-laden fluids
- Excellent dimensional retention under pressure
- Proven performance in high-rate hydraulic fracturing
Limitations:
- Brittle under impact or thermal cycling
- Susceptible to cobalt leaching in chemically aggressive fluids
- Relatively high material cost and manufacturing lead times
Field Insight: In unconventional shale operations, WC plungers are often preferred where abrasive proppants are a leading wear mechanism — particularly in high-SF (sand factor) completions.
Stainless Steel Plungers: Engineering Evaluation
Stainless Steel (SS) plungers offer a versatile and cost-effective option for many upstream applications. Common alloys include 316L for corrosion resistance, 17-4PH for strength and hardness, and Duplex grades for sour service environments involving H₂S.
These materials generally fall in the 180–400 HV range — significantly lower than tungsten carbide — but exhibit better toughness and ductility. This makes them more forgiving under impact loads and thermal cycling.
Advantages:
- Good fatigue resistance under cyclic loading
- Excellent weldability and repair options
- Better availability and shorter lead times
Limitations:
- Faster wear in abrasive conditions
- Limited lifespan in high-chloride or sour gas environments
- Surface roughening can compromise seal efficiency
Operational Use Case: Stainless steel is frequently used in medium-pressure applications or where regular inspection and plunger replacement are feasible — for instance, in fields with scheduled 90-day maintenance intervals.
Ceramic Plungers: Advanced Applications
Ceramic plungers are gaining interest due to their extreme hardness (often >1500 HV) and near-zero wear rates under certain conditions. Materials like Alumina (Al₂O₃), Zirconia (ZrO₂), and Silicon Carbide (SiC) each offer different balances of toughness, corrosion resistance, and cost.
Zirconia, for instance, offers higher fracture toughness than Alumina and better thermal shock resistance. Silicon Carbide excels in highly corrosive fluids but is even more brittle.
Advantages:
- Exceptional wear resistance — ideal for non-abrasive but corrosive environments
- High surface finish quality supports better sealing performance
- Chemically inert in most oilfield fluids
Limitations:
- Brittleness limits use in high-impact environments
- Higher upfront cost and handling requirements
- Prone to chipping or failure during installation if mishandled
Common Application: Ceramic plungers are typically used in injection pumps for water or CO₂ where chemical resistance is paramount but abrasive loading is minimal.
+——————————————————————————————————-+
💡 Quick Takeaways
- Material resilience varies widely: Tungsten Carbide excels in wear resistance, Stainless Steel balances durability and cost, and Ceramics shine in chemical resistance but remain brittle.
- Field context drives material choice: High-sand fracking favors WC, cyclic operations tolerate SS better, and ceramic fits chemical injection roles.
- Material properties must match conditions: Mechanical strength, thermal behavior, and chemical compatibility determine lifecycle success.
+——————————————————————————————————-+
Conclusion
Material selection for pump plungers ( ipumps.com/pump-plungers ) in upstream operations isn’t just a procurement decision — it’s a performance strategy. Each material offers distinct trade-offs in wear resistance, chemical durability, and lifecycle cost. Matching plunger composition to well-specific conditions can dramatically reduce maintenance events and increase pump uptime, with significant implications for TCO and operational efficiency.
Organizations evaluating plunger options may benefit from a formalized selection matrix that compares material behavior against site-specific stressors like abrasive load, temperature variance, and chemical exposure.
Frequently Asked Questions (FAQ)
Q: What material offers the best overall performance for high-pressure fracking operations?
A: Tungsten Carbide is frequently chosen for its abrasion resistance in proppant-heavy environments. However, exact performance depends on fluid composition, pump design, and thermal cycling conditions.
Q: How do temperature cycling conditions affect material selection?
A: Frequent temperature swings can cause brittle materials like ceramics and some grades of WC to crack or spall. Stainless steel’s ductility offers better thermal fatigue resistance, though with shorter wear life.
Frequently Unasked Questions (FUQ)
Q: How does plunger material choice impact seal life and overall pump efficiency?
A: Surface finish and hardness influence seal wear. Smoother, harder materials like ceramics reduce initial friction but may cause accelerated seal wear if brittle particles chip into the seal path.
Q: What are the supply chain considerations for exotic materials during field operations?
A: Materials like WC and ceramics often have longer lead times and stricter handling/storage requirements. This can complicate inventory planning, especially in remote operations with limited logistics support.
Leave a Reply